機(jī)床立柱是機(jī)床重要的結(jié)構(gòu)件,起著支撐橫梁上下運(yùn)動的作用。根據(jù)立柱的結(jié)構(gòu)特點(diǎn)和技術(shù)要求,以及企業(yè)生產(chǎn)實(shí)際,確定了合理的工藝方案,包括鑄件分型面、澆注位置,各類工藝參數(shù)和澆注方法等,生產(chǎn)出合格的大型立車立柱,滿足了立柱的技術(shù)要求。
大型數(shù)控立式車床(以下簡稱“立車”)立柱是機(jī)床的關(guān)鍵基礎(chǔ)零部件,立柱主要對立車橫梁、刀架體及滑枕等參與切削加工的部件起支撐和穩(wěn)定的作用,滿足橫梁沿立柱導(dǎo)軌的Z向運(yùn)動,并在間接承受切削力、振動、溫度變化等惡劣條件下工作。為滿足數(shù)控立式車床的加工要求,立車立柱要求具有足夠高的構(gòu)件強(qiáng)度和剛度,良好的抗振性和抗熱變形能力,所以其結(jié)構(gòu)剛性、減振性能、導(dǎo)軌面硬度等方面要求較高,使得立車立柱的工藝設(shè)計(jì)和生產(chǎn)制造難度較大。
1 立車立柱結(jié)構(gòu)特點(diǎn)及技術(shù)要求
1.1 立車立柱的主要結(jié)構(gòu)特點(diǎn)
立車立柱內(nèi)部是多層結(jié)構(gòu)、強(qiáng)度高,輪廓尺寸大、加工行程長,壁厚不均勻、生產(chǎn)難度大,屬于超大、超重型、高強(qiáng)度灰鑄鐵件。鑄造過程中體積大、結(jié)構(gòu)復(fù)雜,澆注的鐵液量多,鑄件冷卻時間長,易出現(xiàn)縮孔、縮松、氣孔、裂紋、力學(xué)性能不達(dá)標(biāo)等鑄造缺陷,并且生產(chǎn)過程控制難度較大。因此,對工藝設(shè)計(jì)提出了更高的要求。筆者以輪廓尺寸為11 000 mm×2 600 mm×1 250 mm,凈重42 750 kg,毛重46 500 kg,最小壁厚35 mm,最大壁厚154 mm的立車立柱為例展開研究,其結(jié)構(gòu)如圖1所示。
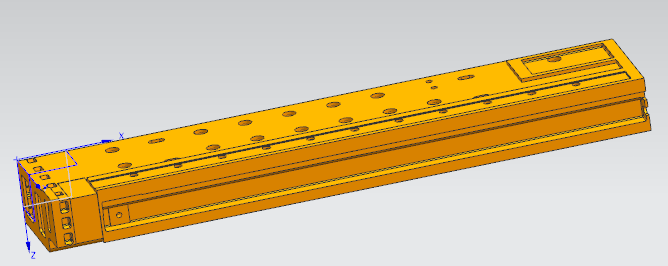
圖1 立車立柱
1.2 立車立柱的技術(shù)要求
鑄件的材質(zhì)為HT250,立柱導(dǎo)軌硬度180~230 HBW,立柱導(dǎo)軌面不允許有縮孔、裂紋、砂眼、夾砂等鑄造缺陷。
根據(jù)立車立柱鑄件結(jié)構(gòu)特點(diǎn)及主要導(dǎo)軌面的技術(shù)要求,從造型材料及造型方式、鑄件的工藝性、分型位置選取、砂芯設(shè)計(jì)、澆注系統(tǒng)設(shè)計(jì)等方面進(jìn)行工藝分析和設(shè)計(jì)。
2.1 造型材料及造型方式
采用樹脂砂生產(chǎn)鑄件具有尺寸精度高、表面光潔度好的優(yōu)勢,但同時也存在易粘砂、易出現(xiàn)氣孔等問題,特別是大型鑄件鐵液量大,凝固時間長,更易產(chǎn)生這些缺陷。因此,在生產(chǎn)中需要控制好再生砂的質(zhì)量,同時增加砂型的排氣,減少砂型的發(fā)氣量。
根據(jù)立柱的結(jié)構(gòu)特點(diǎn)、尺寸大小及實(shí)際生產(chǎn)條件,采用地坑實(shí)樣造型。
2.2 鑄件的工藝性分析
對立柱的鑄造工藝性進(jìn)行分析后發(fā)現(xiàn),立柱背面直角處結(jié)構(gòu)容易開裂,建議設(shè)計(jì)人員采用斜面過渡,同時在壁厚的急劇變化處,增加了工藝?yán)?,以防止裂紋的出現(xiàn)。
運(yùn)用鑄造數(shù)值模擬,分析導(dǎo)致鑄件厚大部位、導(dǎo)軌面等產(chǎn)生縮孔、縮松等缺陷趨勢的原因,優(yōu)化澆注系統(tǒng)、冒口、冷鐵設(shè)計(jì),保證鑄件各部冷卻均衡,以減小鑄造應(yīng)力,防止鑄件產(chǎn)生裂紋和縮孔、縮松缺陷。
2.3 鑄件分型面的選取
分型面的確定應(yīng)考慮:質(zhì)量要求較高的表面應(yīng)放在下面或側(cè)面;鑄件的大平面應(yīng)放在下面;有利于鑄件實(shí)現(xiàn)方向性凝固及便于放置補(bǔ)縮冒口;為減少披縫和錯箱,保證鑄件尺寸及外觀質(zhì)量,鑄件應(yīng)盡量置于同一砂型中。
根據(jù)分型面的選擇原則及立柱的結(jié)構(gòu)特點(diǎn)、技術(shù)要求、生產(chǎn)條件等,為保證立柱導(dǎo)軌面質(zhì)量,以及實(shí)現(xiàn)補(bǔ)縮,立柱的分型面和澆注位置見圖2。
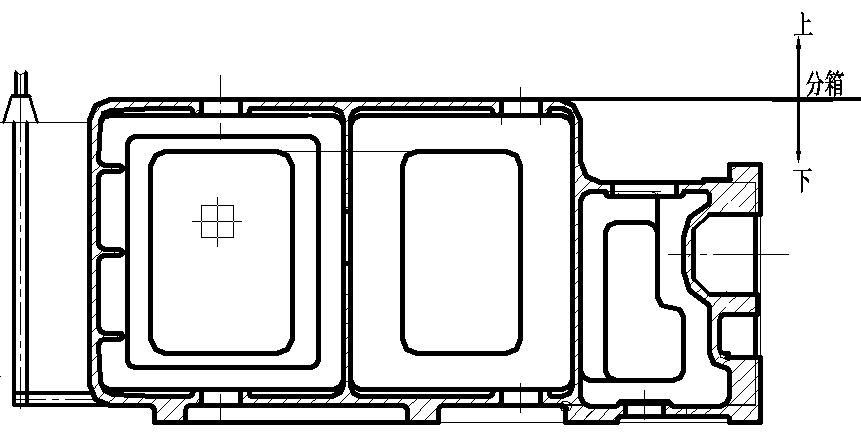
圖2 立柱澆注位置
2.4 鑄件的砂芯設(shè)計(jì)
砂芯設(shè)計(jì)應(yīng)盡量減少砂芯的分割和芯撐的使用;要便于從制芯到下芯的過程和砂芯出氣;另外,砂芯定位要準(zhǔn)確、固定要牢靠。立柱內(nèi)腔結(jié)構(gòu)復(fù)雜、尺寸大,砂芯數(shù)量達(dá)37個,由于兩端砂芯上部沒有出氣孔,因此通過連接側(cè)面的出氣道來排氣。
2.5 鑄件的澆注系統(tǒng)設(shè)計(jì)
立柱澆注系統(tǒng)采用底注式,鐵液從立柱的下平面進(jìn)入型腔,如圖2所示。采用底注式澆注系統(tǒng),金屬液充型較平穩(wěn),液面是逐漸升高的,避免了沖擊、飛濺和氧化,有利于鐵液中雜質(zhì)的上浮及型腔內(nèi)氣體排出,從而有效防止了鑄件導(dǎo)軌產(chǎn)生渣、氣孔等缺陷。
用澆注比速來計(jì)算澆注系統(tǒng)的尺寸。此法可用于各種合金、各類鑄件的澆注系統(tǒng)計(jì)算,主要用在大型和重型鑄件上。
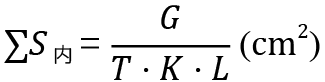
式中,G為流經(jīng)S阻流截面的液體金屬質(zhì)量(kg);T為澆注時間(s);K為單位面積的澆注速度(kg/cm2·s);L為金屬液流動系數(shù)。筆者選取鑄件液體金屬質(zhì)量為52 000 kg,澆注時間為206 s,澆注速度為0.9 kg/cm2·s,金屬液流動系數(shù)取1。
通過公式計(jì)算,同時結(jié)合鑄件結(jié)構(gòu)特點(diǎn)及實(shí)際生產(chǎn)經(jīng)驗(yàn),澆注時要快速充滿鑄型,取∑S內(nèi)=281 cm2。
(b)澆注系統(tǒng)采用半封閉式澆注系統(tǒng)。半封閉式澆注系統(tǒng)充型快,擋渣效果好,不易卷入氣體。根據(jù)實(shí)際生產(chǎn)經(jīng)驗(yàn)公式,∑S直=1.2×∑S內(nèi)=337 cm2;∑S橫=1.4×∑S內(nèi) =393 cm2。
2.6 冒口、冷鐵設(shè)置
立柱導(dǎo)軌和上下端面螺包處壁厚大,易形成縮孔、縮松,需要采用冒口進(jìn)行補(bǔ)縮,為保證兩導(dǎo)軌補(bǔ)縮順暢,兩導(dǎo)軌之間還采用過道進(jìn)行連接。為防止縮孔、縮松,立柱共設(shè)置了方形明冒口20個。
為防止縮孔、縮松,保證立柱導(dǎo)軌組織致密和冒口的補(bǔ)縮距離,在導(dǎo)軌等厚大部位設(shè)置外冷鐵進(jìn)行激冷,整個立柱共放置了256塊外冷鐵。
2.7 其他工藝參數(shù)的選擇
根據(jù)實(shí)際生產(chǎn)經(jīng)驗(yàn),鑄件收縮率為1%。
根據(jù)鑄件尺寸大小、結(jié)構(gòu)特點(diǎn),鑄件的機(jī)械加工余量按GB/T 6414-2017選取。
根據(jù)鑄件的結(jié)構(gòu)特點(diǎn)及環(huán)境條件,選取開箱時間為澆筑后368 h,選取立柱的保溫時間為392 h。
針對優(yōu)化后的工藝設(shè)計(jì),編制鑄件生產(chǎn)過程控制方案和現(xiàn)場施工方案,跟蹤生產(chǎn)過程,確保澆冒系統(tǒng)等與工藝要求一致,做好工藝驗(yàn)證工作。
3.1 造型、合箱控制
(1)造型控制
根據(jù)要求使用合格的型、芯砂,保證型、芯砂24 h抗拉強(qiáng)度不低于0.8 MPa。造型、制芯過程填砂時,采用分層填砂。每層厚度控制在200 mm左右,用木棒等充分緊實(shí),砂型不易到達(dá)的部位用手搗實(shí)。砂芯修整完清理干凈后放置4 h以上,采用流涂方式涂刷醇基涂料,砂型在起模4 h后涂刷醇基涂料,保證涂料的厚度約為1 mm,易粘砂部位應(yīng)適當(dāng)加厚。
合箱前要驗(yàn)箱,確保分型面及出氣芯頭坭條充分壓實(shí),保證蓋箱等出氣孔通暢,合箱后正確放置澆口杯,使?jié)部诒c蓋箱直澆道對齊,并防止雜物進(jìn)入澆冒口系統(tǒng)及型腔。
3.2 熔化、澆注方案
根據(jù)鑄件的材質(zhì)及結(jié)構(gòu)確定化學(xué)成分,見表1,保證鑄件性能達(dá)到設(shè)計(jì)要求。
表1 立柱熔煉時化學(xué)成分(質(zhì)量分?jǐn)?shù),%)

(2)澆注方案
澆注時采用兩包澆注,兩包鐵液溫度要盡量一致,溫差不超過20 ℃。出爐溫度>1 450 ℃,澆注溫度控制在1 320~1 340 ℃。
采用上述造型、扣箱、澆注等方案生產(chǎn)出來的立車立柱,加工后情況如圖3所示,鑄件沒有出現(xiàn)縮孔、縮松、裂紋等鑄造缺陷,試棒檢測、本體檢測金相組織和力學(xué)性能均符合GB/T 9439-2010、GB/T 7216-2009要求。目前已按此方案進(jìn)行批量生產(chǎn)。
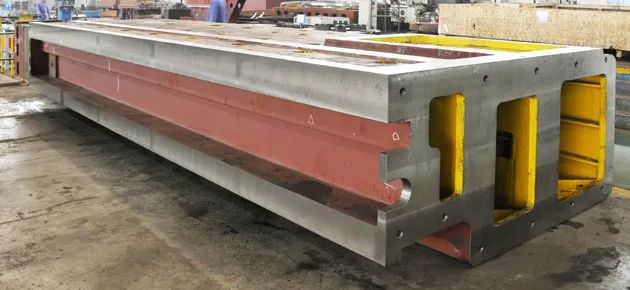
圖3 立柱加工后情況
大型數(shù)控立式車床的立柱由于尺寸長,內(nèi)部結(jié)構(gòu)復(fù)雜、筋板多且分層,鐵液充型的行程較長、鑄件冷卻時間長,易產(chǎn)生冷隔、縮孔、縮松、氣孔、裂紋、力學(xué)性能不達(dá)標(biāo)等鑄造缺陷。對于這種大型鑄件的生產(chǎn),要結(jié)合實(shí)際生產(chǎn)條件、生產(chǎn)能力、零件的技術(shù)要求、結(jié)構(gòu)特點(diǎn)等各方面的因素進(jìn)行工藝分析和優(yōu)化,確定合理的鑄造工藝方案、同時嚴(yán)格控制生產(chǎn)過程,才能確保鑄件的質(zhì)量達(dá)到設(shè)計(jì)要求。